CrCN – The Coating With
Exceptional Adhesion Strength.
CrCN coatings are the number one choice for all those areas of application demanding, above all, abrasion, corrosion and oxidation resistance as well as a low friction coefficient. CrCN coatings also excel through exceptional adhesion strength, excellent chemical resistance, high temperature resistance in the open air and low levels of tension. These coating systems show good sliding properties at minimal lubrication. High degrees of hardness at very low brittleness allow for the deposition of thicker CrCN coatings (up to 10 µm) with very good adhesion properties.
CrCN – The Coating With
Exceptional Adhesion Strength.
CrCN coatings are the number one choice for all those areas of application demanding, above all, abrasion, corrosion and oxidation resistance as well as a low friction coefficient. CrCN coatings also excel through exceptional adhesion strength, excellent chemical resistance, high temperature resistance in the open air and low levels of tension. These coating systems show good sliding properties at minimal lubrication. High degrees of hardness at very low brittleness allow for the deposition of thicker CrCN coatings (up to 10 µm) with very good adhesion properties.
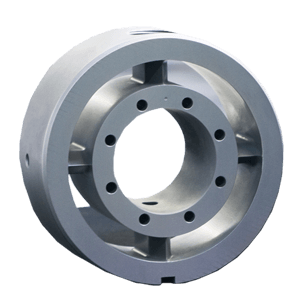
CrCN – Chrome Carbon Nitride Performance Parameters.
CrCN – Chrome Carbon Nitride Performance Parameters.
Hardness
2.300 ± 200 HV
Maximum working temperature
600 °C / 1.110 °F
Friction coefficient against steel
0,3 – 0,4
Coating thickness
2 – 6 µm (possible up to 10 µm)
Colour
silver-grey
DUPLEX
available
Low-temperature method
available
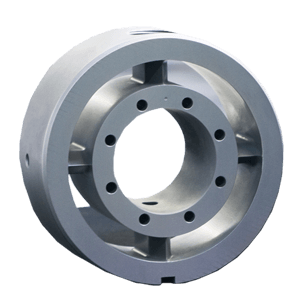
CrCN – Preferred Areas of Application
- Metal forming
- Plastic processing
- Aluminium and magnesium pressure die casting
Perfect for Plastic Processing and Forming
In the area of plastic processing, CrCN coatings are applied to tools subject to corrosive and abrasive wear, e.g. due to aggressive and hard filler materials. Combined with a polish, CrCN contributes to improved removal from the mould. In plastic injection moulding (processing of PVC or fire proofing), deposit formation is significantly reduced.
Forming & Co.
CrCN coatings are predominantly used on drawing, punching, pressing and forming tools for the machining of non-ferrous metals. Especially for titanium and copper alloys. Additionally, these coating systems are used in aluminium and magnesium pressure die casting, e.g. for mould inserts and cores requiring increased levels of corrosion protection.
One of the areas of application of CrCN coatings is the machining of copper and other non-ferrous materials. This coating protects milling tools, lathes, drilling and cutting tools when machining non-ferrous metals – especially those consisting of titanium and copper alloys.
Application of CrCN by means of the DUPLEX method or the low temperature method is available.
Is CrCN the right coating for your area of application? Or would one of our numerous other hard coatings be even better suited for your individual requirements?
Which coating system is the perfect match? We will gladly advise you!